Tungsten Carbide Composite Rollers Binding Methods
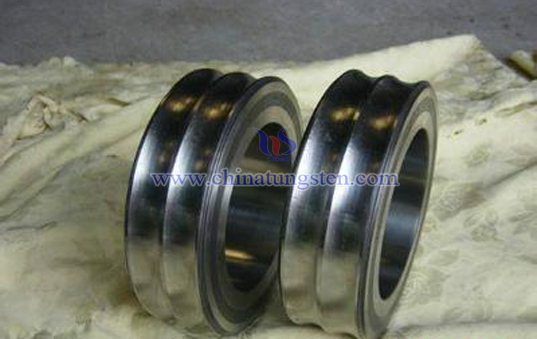
Preparation key tungsten carbide composite rollers is a combination of inner and outer layers. Its combination of methods are mechanical bonding, thermal loading method, cementation, hot isostatic pressing, casting, welding method. Among them, the thermal loading method is the use of the inner interference, leaving the inner and outer layers are held together by shrink fitting. However, cemented tungsten carbide outer ring must have a certain thickness, so as not to rupture under the action of inner tension. Therefore using this method of production of a composite roll, savings which tungsten carbide is limited. Cementation method using epoxy glue like the inner and outer rings bonded together. Prepared by this method should not be used in a composite rollers under high temperature and high pressure.
Tungsten carbide composite rollers casting (including centrifugal casting method) before casting, powder metallurgy process of preparation of the first outer ring tungsten carbide, and in conjunction with the torus, pre-coated with a layer of metal as a transition layer . The inner ring with steel, cast iron, with casting method in conjunction with the outer ring as a whole, namely tungsten carbide composite roller. According to the working conditions and user requirements rollers use different methods to produce composite roll. But tungsten carbide composite rollers substrate to ensure rational use of complex tungsten carbide composite rollers overall performance is critical, common substrate for selection of three categories: gray iron, ductile iron, cast steel.
Welding by heating in a vacuum furnace, so that between the inner and outer rings of molten solder preset, the inner and outer ring combined into one. Also by plasma spray, cored electrode surfacing tungsten carbide powder by means of the welding on steel inner ring, forming a hard metal shell, get tungsten carbide composite roller, and then machined to become composite roll. But welding tungsten carbide powder content is restricted, thus lower the hardness of the outer ring, the higher porosity. The use of "cast welding" method is to clean the surface tungsten carbide, coated with a low melting point of the solder, into the mold cavity, the use of liquid metal heat to low melting point alloy tungsten carbide surface melting, solidification after the formation of a certain buffer layer, so that the tungsten carbide and the cast alloy together to form a cemented tungsten carbide composite roller.